
Tercer Milenio
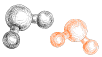
En colaboración con ITA
Proyecto DIGIFUS 4.0
Fabricación aditiva: un gemelo digital para gastar menos energía y material al unir metales
Itainnova trabaja en un modelo virtual de procesos de fabricación aditiva para incrementar la eficiencia energética y reducir el consumo de material.
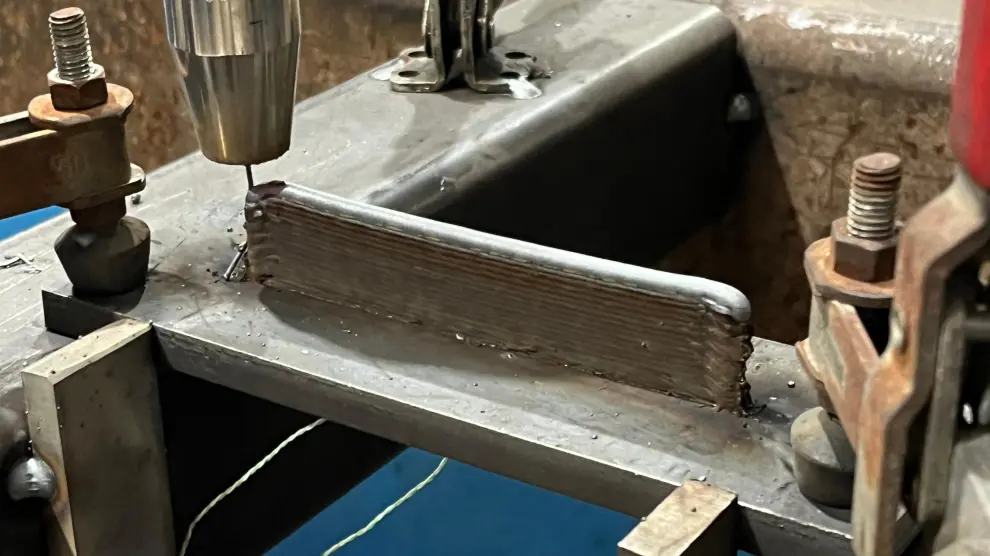
La fabricación aditiva es, hoy en día, una de las tecnologías estrella en el escenario de la transformación digital. Pase lo que pase, ya sean años y años, tensiones o condiciones adversas, tanto la soldadura como la fabricación aditiva comparten la necesidad de ser fieles a una promesa: que nada las separe porque han generado una unión resistente mecánicamente y con propiedades estables. Su responsabilidad es grande, especialmente en sectores como la industria aeroespacial, donde la fabricación aditiva se quiere emplear en la creación de componentes ligeros y complejos, garantizando la seguridad y el rendimiento de las aeronaves.
Entre los procesos de fabricación aditiva, encontramos la deposición de energía focalizada WAAM. ¿En qué consiste? "Es como construir algo capa por capa usando un arco eléctrico que funde y pega cordones de metal", explica Carlos Mallor, del equipo de Integridad estructural y fatiga del Departamento de Tecnologías Materiales y Componentes de Itainnova. Esta técnica permite construir piezas tridimensionales. "Por ejemplo, en lugar de cortar y unir placas de metal, podemos crear directamente la pieza final. Es como una impresora 3D, pero con metal –describe gráficamente–, y ayuda a hacer cosas más eficientes y de alta calidad". En el futuro, "se pretende utilizar ampliamente en diferentes industrias como la aeroespacial, donde garantizar la seguridad y a la vez optimizar la relación resistencia-peso de los componentes es crucial".
Para ofrecer estas garantías, es fundamental comprender cómo varía la calidad en la deposición de capas sucesivas. La digitalización y simulación de estos procesos, como propone el proyecto Digifus 4.0, en el que participa Itainnova, "son esenciales para analizar la robustez de estas uniones y optimizar los parámetros de fabricación, garantizando propiedades mecánicas duraderas", señala Susana Calvo, responsable del equipo de Integridad estructural y fatiga, del Departamento de Tecnologías Materiales y Componentes. "Estos desarrollos –concreta– permiten un control preciso y consistente de los procesos de fabricación, reducen desperdicios y fomentan una mejora continua".
El objetivo es generar un gemelo digital que represente procesos de fabricación basados en la deposición de energía focalizada para metales. El resultado final será "un modelo de simulación integral que analice la viabilidad de fabricación, determine parámetros óptimos y estime indicadores de calidad de las piezas producidas", destacan los técnicos de Itainnova. "Al enfocarse en la caracterización de la fuente de calor, en la variabilidad del proceso y en la simulación detallada –explican–, el proyecto aspira a avanzar significativamente en la comprensión y optimización de la fabricación aditiva WAAM, contribuyendo así al desarrollo de soluciones innovadoras y sostenibles para la producción de componentes metálicos".
Generar un conocimiento más profundo del proceso permitirá relacionar variables como velocidad, temperatura, cantidad de material de aporte, trayectorias de deposición, etc. con estándares de calidad y criterios medioambientales tales como un mínimo uso de material y consumo energético.
El proyecto
- Nombre Digifus 4.0. Digitalización de procesos de fabricación basados en deposición de materiales metálicos por energía focalizada para incrementar la eficiencia energética y reducir el consumo de material: soldadura y fabricación aditiva.
- Objetivo Generar un gemelo digital de procesos de fabricación basados en deposición por energía focalizada para materiales metálicos orientado a analizar factibilidad de fabricación, determinar parámetros óptimos y estimar indicadores de calidad de piezas fabricadas.
- Participantes El presente proyecto es fruto de la cooperación entre la Agrupación Empresarial Innovadora (AEI) Asociación Aeronáutica Aragonesa, la AEI Clúster de Automoción de Aragón, y las entidades Alot Metal, S.L., Galagar Welding, S.L. y el Instituto Tecnológico de Aragón.
Validación experimental de los modelos, capa a capa
En el proyecto Digifus 4.0, Itainnova aporta su experiencia y recursos en investigación tecnológica, contribuyendo al desarrollo de un gemelo digital para procesos de fabricación basados en deposición por energía focalizada.
Para crear ese modelo digital, entra en juego la aplicación de técnicas de digitalización y simulación, pero también es necesario el análisis experimental en el laboratorio. Todo ellos "con el objetivo de avanzar en la comprensión de la variabilidad del proceso y optimizar la calidad de las piezas fabricadas, consolidando así el conocimiento necesario para la evolución de las tecnologías de fabricación aditiva", indica Carlos Mallor.
Hasta el momento, ya se han realizado algunas campañas experimentales y se han recopilado datos suficientes para desarrollar las simulaciones del proceso.
Paso a paso, capa a capa, el proyecto avanza. Dentro y fuera del ordenador. "Se ha adoptado una estrategia donde se irá incrementando progresivamente la complejidad de los componentes a fabricar", explica Mallor. Para ello, se realizó una primera caracterización de la fuente de calor, se fabricó y simuló la adición de material para una única capa, como primera capa de una geometría 3D, y también se fabricó y simuló la adición de veinte capas para formar una pared delgada. En ambos casos, explica el ingeniero de Itainnova, "se monitorizó la temperatura mediante la técnica de termografía, así como mediante termopares" (un termopar es un dispositivo para medir temperaturas, basándose en la diferencia de potencial originada por el calor en la unión de dos metales distintos). También se caracterizó la zona afectada térmicamente por metalografía.
Ambas acciones forman parte del plan de validación experimental de los modelos para generar un gemelo digital del proceso. Las próximas acciones por desarrollar incluyen investigaciones experimentales que se centrarán en la caracterización de la construcción de piezas cada vez más complejas, así como en su simulación detallada. También se avanzará en la cuantificación del comportamiento mecánico y funcional de las piezas obtenidas mediante fabricación aditiva.
-Ir al suplemento Tercer Milenio
Apúntate y recibe cada semana en tu correo la newsletter de ciencia